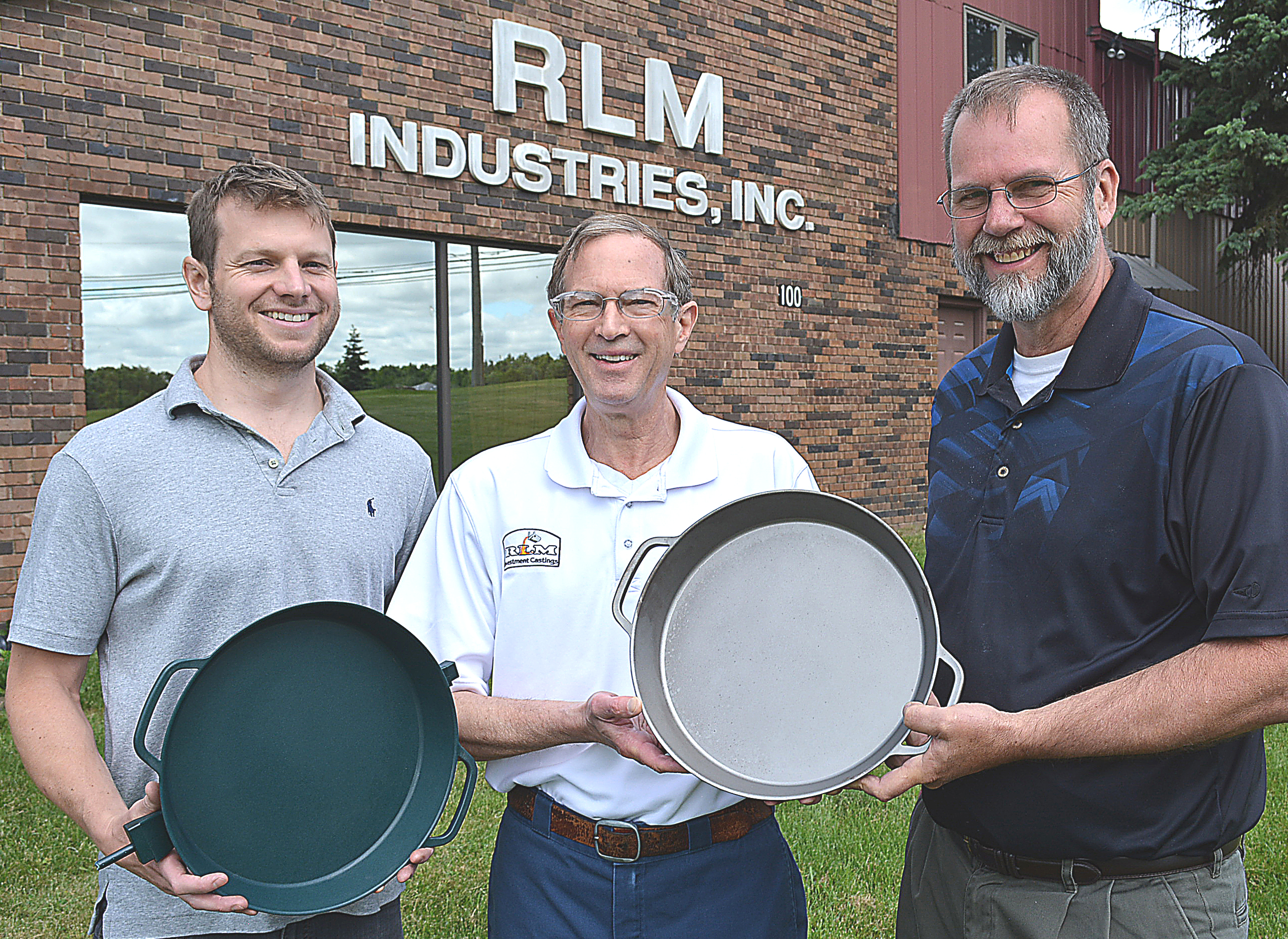
Oxford’s small manufacturing community produces a variety of parts and products for the private and public sectors.
And now it’s added cookware to the list.
RLM Industries, Inc., located in a 64,000-square-foot facility at 100 Hummer Lake Rd., is producing cast-iron skillets for the Royal Oak-based Marquette Castings LLC.
“We’ve never made cookware (before),” said Rick Meachum, vice president of engineering and sales for RLM Industries.
“Auto, heavy construction and military are our three top markets. It doesn’t seem like (cookware) fits in, but it (does). It’s actually been a fun project because it’s (not) our ordinary, run-of-the-mill stuff.”
RLM is currently producing a 10.5-inch skillet and a 13-inch pan.
Cast-iron skillets are typically manufactured using a process known as sand casting, which involves pouring molten metal into a mold made from sand.
But that’s not how RLM makes them. The company, which was founded in 1975 and employs approximately 76 people, uses what’s known as investment casting.
“Investment casting is the top-of-the-line of all the casting processes,” said Meachum, who’s been with RLM for 41 years. “That’s really what separates us from everybody (else).”
“As far as I know we’re the first company to actually ever use investment casting to make cast-iron skillets. It’s totally unique in that regard,” said Eric Steckling, cofounder and CEO of Marquette Castings.
“Cookware isn’t your typical investment casting project,” Meachum noted.
Investment casting starts with using an aluminum die to create a reverse image of the item to be cast. This die is injected with wax to create a pattern that gets clustered and mounted onto a sprue (or tree), the passage through which molten material is later introduced into a mold.

This cluster of wax patterns on the sprue then gets repeatedly dipped in liquid ceramic. About eight coatings are used, according to Meachum, to form a shell around the entire tree that’s about three-eighths-of-an-inch thick.
Meachum said the empty ceramic shell is placed into a 1,400-degree burnout oven that removes all the wax. The shell is then loaded into an 1,800-degree preheat oven where it’s baked for three hours.
Molten metal is poured into the ceramic mold where it cools and solidifies into the finished product.
This process has created a superior cast-iron skillet, according to Steckling and Meachum.
For one thing, RLM’s pans are smoother.
“Smoother surfaces are just easier to cook on and clean,” said Steckling, who’s an alumnus of Kingsbury Country Day School in Addison Twp. “(They’re) also a little easier to maintain.”
The skillets produced by RLM are significantly lighter than other cast-iron skillets.
Meachum explained that’s because sand casting creates a pan with a “really thick wall” whereas investment casting produces a “much thinner wall” that yields “the same results,” but with “much less” weight.
“Fact is, it may even heat up a little faster because the heat doesn’t have to go through so much metal before it actually reaches the food. The heating is more consistent,” he said.
Because investment casting isn’t cheap neither are Marquette Castings’ skillets.
The 10.5-inch pan sells for $195, while the 13-inch one runs $225.
“(They’re) paying a premium for this process, but they feel it’s well worth the investment,” Meachum said.
“There’s some people out there that want the best (skillet) and that’s what we’re making,” said Steckling, who noted the smooth surface and lighter weight are traits that “just really aren’t achievable with other (casting) methods right now.”
Steckling sees his company’s pans as things that will last a “lifetime and beyond.”
“This is a piece we intend our customers to have and use forever,” he said. “We like to say it’s something you’re going to be able to pass down (to future generations).”
Unlike some items in the kitchen, Marquette Castings’ skillets aren’t meant to spend most of their time hibernating in cabinets, waiting to be used for certain dishes or special occasions. Steckling believes they can be pressed into service “every single day.”
“The great thing about cast iron is it’s so versatile,” he explained. “You can use it every day because it pretty much excels at any type of cooking method.”
A person can use it to cook bacon and eggs in the morning and make a steak or a stir-fry for dinner. It’s even great for baking classics like corn bread and pizza.
“There’s not really a lot that it can’t do,” Steckling noted.
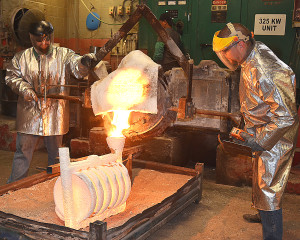
Meachum indicated he loves cast-iron cookware and uses it whenever he can.
“When you season these things right, they’re as good as any teflon-coated pan that’s out there,” he said. “An egg will just slide across the surface.”
Marquette Castings previously worked with foundries in China to manufacture skillets using investment casting, but Steckling wasn’t pleased with the results.
“The quality we have now with these (from RLM) is much better,” he said.
But it wasn’t just the lack of quality overseas that motivated Marquette Castings to seek a new manufacturer.
According to Steckling, his customers were requesting American-made products.
“That was a big, driving force as well,” he said.
Prior to RLM, Steckling tried using another foundry in Michigan, but things didn’t go so well and they didn’t make much progress.
“I could tell we were a long way from the finish line in terms of actually getting the product we were looking for,” he said.
Fortunately, RLM was able to deliver the goods.
“I was really impressed when I saw what they came up with (regarding) how to cast these,” Steckling said.
For example, thanks to RLM’s use of robotics, the company is able to dip 12 wax patterns at a time into the liquid ceramic. The other Michigan foundry was only able to dip two at a time because they were doing it by hand.
“These guys really have their processes in order and they do a good job,” Steckling noted. “We’re finally at the spot where I’m really happy with what we’re making.”
Other companies that may be interested in using RLM Industries to make their cast-iron cookware are out of luck.
“The door’s basically closed as far as doing it for anybody else,” Meachum said. “We have an agreement that we’ll not do any work for their competition and they’ll give us all of their investment casting work. So, it’s truly a partnership between us.”
To learn more about Marquette Castings, please visit www.marquettecastings.com.
More information about RLM Industries can be found at www.rlmcastings.com.
Hi CJ – Your writing ability is amazing. Thank you for the job you did on the cookware article. From the activity I am hearing around RLM I think your paper sales will increase this week. Everyone here plans on buying about 5 copies. LOL
Thank you, Rick. I appreciate that very much. Your company is truly a great asset to this community.
I found it interesting to read about unique Oxford industry. I worked for a cookware company for several years and can see the value in RLM’s process. Thanks for sharing!